Spirulina, a blue-green algae, is a versatile and valuable resource that can address malnutrition and support food security. Its adaptability to various agricultural and food processing methods makes it a versatile and valuable resource. Spirulina is a nutritional powerhouse, rich in proteins, vitamins, minerals, energy, phytonutrients, fatty acids, carbohydrates, and electrolytes.
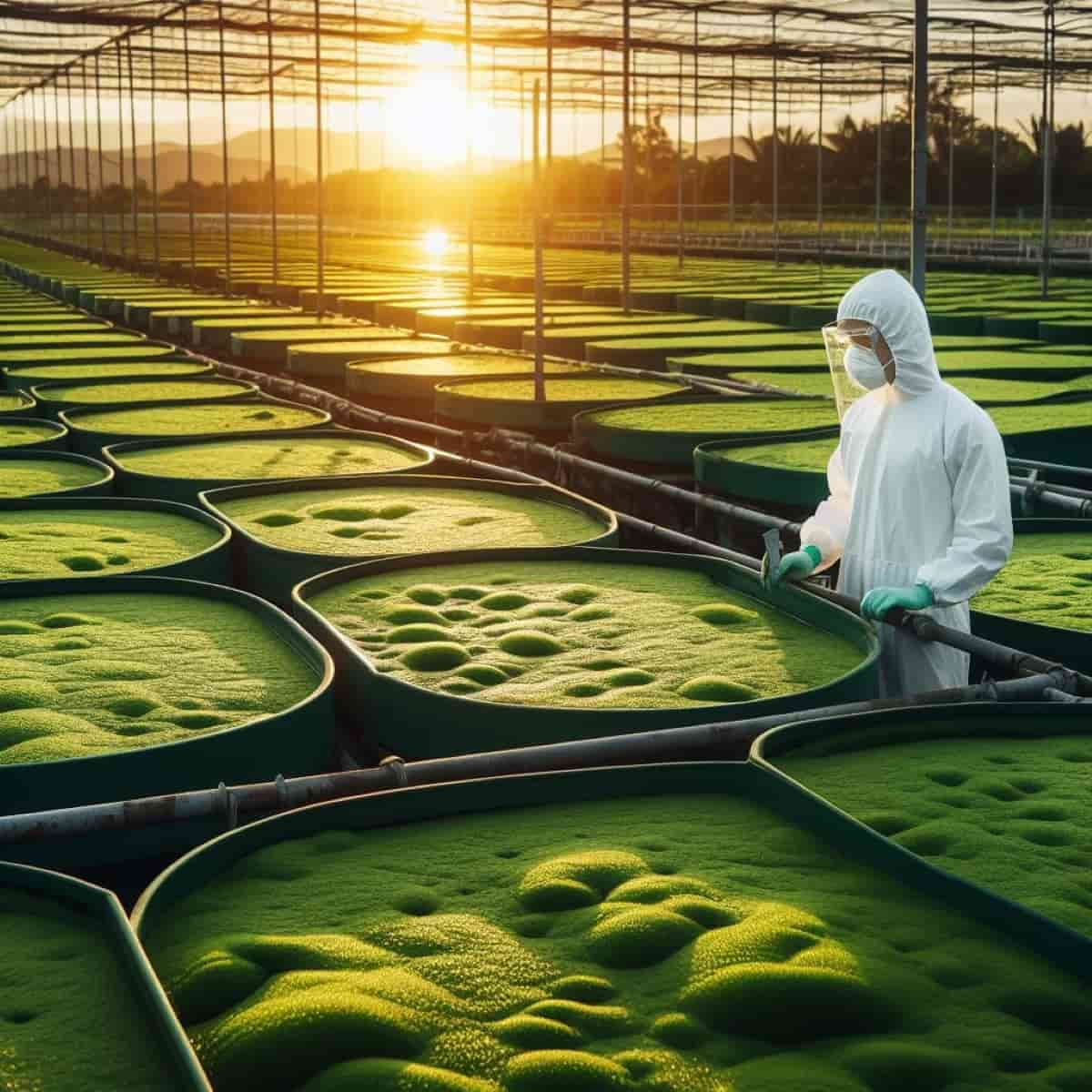
Cost of Spirulina Cultivation
Spirulina the Nutritional Algae for a Healthier Future
Spirulina is a natural supplement with numerous health benefits, including eradicating malnutrition, boosting the immune system, enhancing anti-viral and anti-aging activity, reducing cancer risk, reducing kidney toxicity, improving wound healing, aiding in weight loss, acting as a natural detoxifier, anti-diabetic activity, cellular nourishment, blood purification, treatment of anemia, and balancing blood chemistry.
Its applications extend beyond human nutrition, including animal feed, fish and prawn cultivation, and organic manure. Spirulina is cultivated in tanks with a pH between 9.5 to 10.8, using a mix of NPK formulation, magnesium sulfate, and sodium bicarbonate for nourishment. Harvesting occurs from the 15th or 16th day, with the thick mass filtered, shade-dried, and transformed into fine powder. This powder can be processed into various products like tablets, capsules, biscuits, or chikki.
Cost of Spirulina Production Equipment
The cost of spirulina production equipment, including containers, pumps, filters, aerators, heaters, thermometers, pH meters, and harvesters, depends on the scale and method of production. There are three methods: open pond system, closed photobioreactor system, and hybrid system. A study by the Central Food Technological Research Institute (CFTRI) found that the cost of equipment for an open pond system with a 10 kg per day production capacity is around Rs 2.5 lakh. In comparison, the cost for a closed photobioreactor system with 1 kg per day is around Rs 10 lakh.
Cost of Raw Materials and Nutrients
The cost of raw materials and nutrients for spirulina cultivation depends on the availability and quality of these inputs in the local market. The cost of water, carbon source, nitrogen source, phosphorus source, potassium source, magnesium source, iron source, and trace elements should be free from contaminants and have a pH of 9-10. The cost of these inputs depends on the production capacity of the system. For an open pond system with a 10 kg per day production capacity, the cost is about Rs 1.5 lakh per year. For a closed photobioreactor system with a 1 kg per day production capacity, the cost is about Rs 3 lakh per year.
In case you missed it: Spirulina Production Process: Exploring From Cultivation to Harvesting and Drying

Energy Costs
The third cost to consider is the energy costs, which include the electricity and fuel costs for running the pumps, filters, aerators, heaters, and harvesters. The energy costs depend on the type and size of the equipment, the duration and frequency of operation, and the local tariff rates.
The energy costs for an open pond system with a production of 10 kg per day is about Rs 1 lakh per year. The energy costs for a closed photobioreactor system with a production capacity of 1 kg per day is about Rs 2 lakh per year. The energy costs for a hybrid system with a production capacity of 5 kg per day is about Rs 1.5 lakh per year.
Labor Costs
The fourth cost to consider is the labor costs, which include the wages and salaries of the workers involved in spirulina cultivation, harvesting, processing, and packaging. The labor costs depend on the number and skill level of the workers, the hours and days of work, and the local wage rates.
The labor costs for an open pond system with a production of 10 kg per day is about Rs 2 lakh per year. The labor costs for a closed photobioreactor system with a production capacity of 1 kg per day is about Rs 3 lakh per year. The labor costs for a hybrid system with a production capacity of 5 kg per day is about Rs 2.5 lakh per year.
Maintenance and Repair Costs
The fifth cost to consider is the maintenance and repair costs, which include the costs of cleaning, servicing, repairing, and replacing the equipment and parts. The maintenance and repair costs depend on the quality and durability of the equipment and parts, the frequency and intensity of use, and the availability and cost of spare parts.
The maintenance and repair costs for an open pond system with a production capacity of 10 kg per day are about Rs 50,000 per year. The maintenance and repair costs for a closed photobioreactor system with a production capacity of 1 kg per day is about Rs 1 lakh per year. The maintenance and repair costs for a hybrid system with a production capacity of 5 kg per day are about Rs 75,000 per year.
Cost of Water Treatment and Waste Management
The sixth cost to consider is water treatment and waste management, which includes treating water used for spirulina cultivation, disposing of waste, and complying with environmental regulations. The cost depends on the quality and quantity of water and waste, the efficiency of treatment and disposal methods, and local environmental standards and fees.
In case you missed it: Cultivating Green Gold: Exploring the Potential of Spirulina Contract Farming
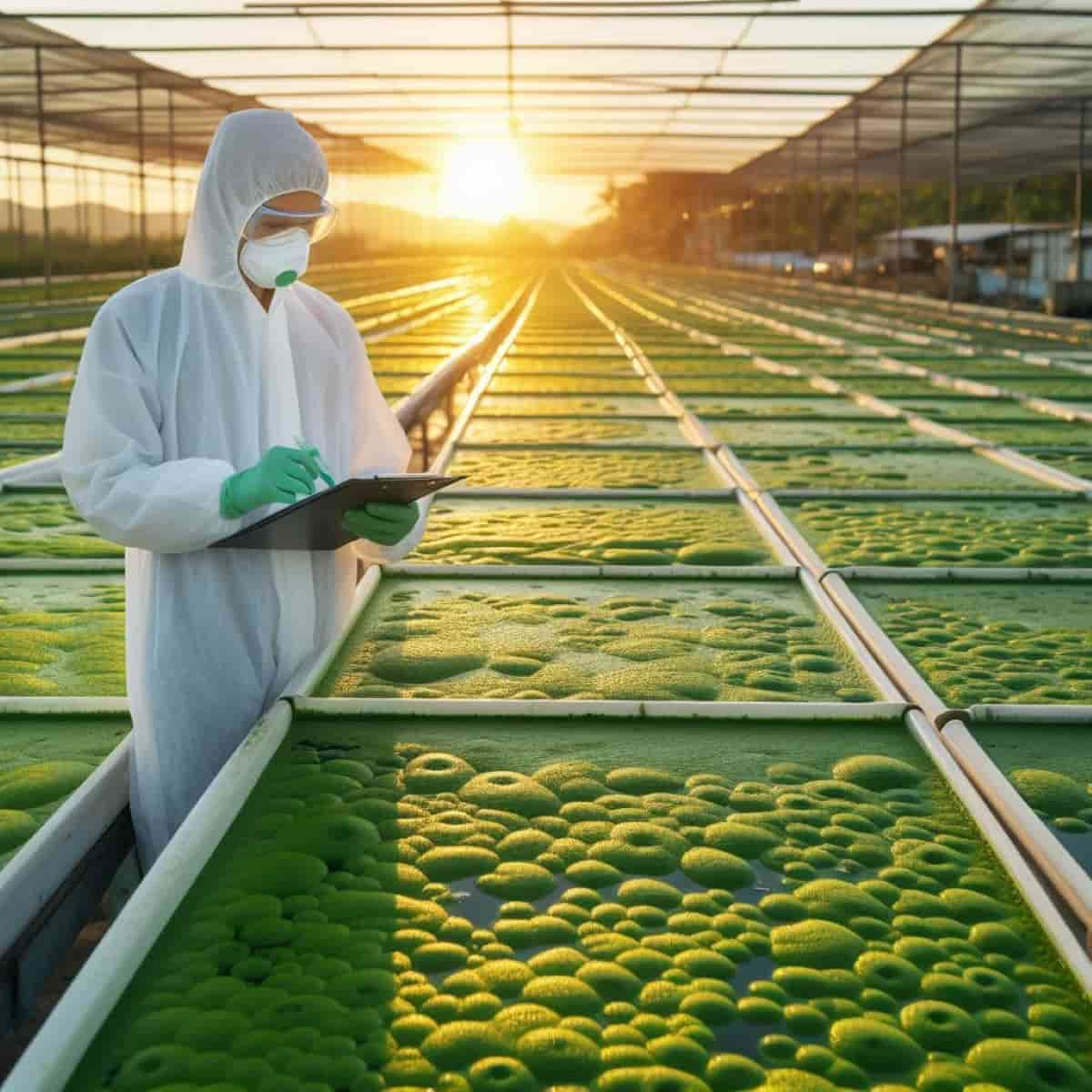
The cost of water treatment and waste management for an open pond system with a 10 kg per day production capacity is about Rs 25,000 per year, while for a closed photobioreactor system with a 1 kg per day production capacity, it is about Rs 50,000 per year.
Cost of Quality Control and Testing
The cost of quality control and testing for spirulina products is a crucial factor to consider. This includes testing the quality and safety of the products, obtaining certifications from authorities, and maintaining quality standards. The cost depends on the quality and quantity of the products, the type and frequency of testing methods, and local certification requirements and fees.
The cost of quality control and testing for an open pond system with a 10 kg per day production capacity is around Rs 25,000 per year, Rs 50,000 per year for a closed photobioreactor system, and Rs 37,500 per year for a hybrid system.
Cost of Transportation and Distribution
The cost of transportation and distribution of spirulina products, including transportation, packaging, storage, and marketing, is a crucial factor to consider. The cost depends on factors like distance, mode of transportation, packaging type and size, storage duration, and marketing strategy. A study by CFTRI shows that an open pond system with 10 kg per day costs about Rs 50,000 per year, a closed photobioreactor system with 1 kg per day costs about Rs 1 lakh per year, and a hybrid system with 5 kg per day costs about Rs 75,000 per year.
Total Cost of Spirulina Cultivation
Cost Component | Open Pond System (10 kg/day) | Closed Photobioreactor System (1 kg/day) | Hybrid System (5 kg/day) |
Equipment | Rs 2.5 lakh | Rs 10 lakh | Varies |
Raw Materials & Nutrients | Rs 1.5 lakh per year | Rs 3 lakh per year | Rs 2 lakh per year |
Energy | Rs 1 lakh per year | Rs 2 lakh per year | Rs 1.5 lakh per year |
Labor | Rs 2 lakh per year | Rs 3 lakh per year | Rs 2.5 lakh per year |
Maintenance & Repair | Rs 50,000 per year | Rs 1 lakh per year | Rs 75,000 per year |
Water Treatment & Waste Management | Rs 25,000 per year | Rs 50,000 per year | Varies |
Quality Control & Testing | Rs 25,000 per year | Rs 50,000 per year | Rs 37,500 per year |
Transportation & Distribution | Rs 50,000 per year | Rs 1 lakh per year | Rs 75,000 per year |
Total Cost | Rs 8.5 lakh per year | Rs 20 lakh per year | Rs 12 lakh per year |
In case you missed it: Frequently Asked Questions About Spirulina Farming

Conclusion
The cost of spirulina cultivation in India encompasses a spectrum from equipment to quality control, with significant variations across systems. Open pond systems are the most economical, while closed photobioreactors entail higher costs, reflecting their advanced technology. Hybrid systems offer a balanced cost-efficiency, catering to diverse production needs.
- Feed Your Flock for Less: Top 10 Tips to Save on Chicken Feed
- Ultimate Guide to Ossabaw Island Hog: Breeding, Raising, Diet, and Care
- Hatching Answers: The Top 10 Reasons Your Chickens Aren’t Laying Eggs
- Eggs and Economics: Breaking Down the Cost of Raising Backyard Chickens
- Defend Your Greens: Proven Methods to Keep Iguanas Out of Your Garden
- Ultimate Guide to Cinnamon Queen Chicken: A Comprehensive Guide for Beginners
- Ultimate Guide to California Tan Chicken: Breeding, Raising, Diet, Egg-Production and Care
- Ultimate Guide to Marsh Daisy Chicken: Breeding, Raising, Diet, and Care
- 10 Types of Chicken Farming Businesses You Can Start for Profits